Brentwood, Tn. Blower Door Code Requirement
If you're attempting to comply with Brentwood Tennessee ICC International Residential Code, 2012 edition - International Energy Conservation Code, 2009 Edition:
Residential Final Inspection Checklist - City of Brentwood, T.
2012 International Residential Code for One- and Two-Family Dwellings (IRC) 2012 edition with 2009 ICC IECC
Effective January 1, 2013
Blower door test passed and 3rd party test certification received R403.1
Are testing complies with IECO 2009-2012 requirements.
Air leakage testing is a quantitative requirement but does not identify the source of excessive leakage. We'll provide additional analysis to locate the source of excessive leakage so repairs can be conducted to comply with IRC requirements.
Looking for ICC, IECC, IRC, 2009 - 2012 building international energy conservation code compliance testing in Brentwood, TN?
Have requirements from 2009
ICC International Residential Code, 2012 edition - International Energy Conservation Code, 2009 Edition
402.4 Air leakage (Mandatory).
402.4.1 Building thermal envelope. The building thermal envelope shall be durably sealed to limit infiltration. The sealing methods between dissimilar materials shall allow for differential expansion and contraction. The following shall be caulked, gasketed, weatherstripped or otherwise
sealed with an air barrier material, suitable film or solid material:
1. Alljoints, seams and penetrations.
2. Site-built windows, doors and skylights.
3. Openings between window and door assemblies and their respective jambs and framing.
4. Utility penetrations.
5. Dropped ceilings or chases adjacent to the thermal envelope.
6. Knee walls.
7. Walls and ceilings separating a garage from conditioned spaces.
8. Behind tubs and showers on exterior walls.
9. Common walls between dwelling units.
10. Attic access openings.
11. Rim joist junction.
12. Other sources of infiltration.
402.4.2 Air sealing and insulation. Building envelope air
tightness and insulation installation shall be demonstrated
comply with one of the following options given by Section
402.4.2.1 or 402.4.2.2:
402.4.2.1 Testing option. Building envelope tightness and insulation installation shall be considered acceptable when tested air leakage is less than seven air changes per hour (ACH) when tested with a blower door at a pressure of 33.5 psf (50 Pa). Testing shall occur after rough in and
after installation of penetrations of the building envelope, including penetrations for utilities, plumbing, electrical, ventilation and combustion appliances.
During testing:
1. Exterior windows and doors, fireplace and stove doors shall be closed, but not sealed;
2. Dampers shall be closed, but not sealed, including exhaust, intake, makeup air, backdraft and flue
dampers;
3. Interior doors shall be open;
4. Exterior openings for continuous ventilation systems and heat recovery ventilators shall be closed
and sealed;
5. Heating and cooling system (s) shall be turned off;
6. HVAC ducts shall not be sealed; and
7. Supply and return registers shall not be sealed.
402.4.2.2 Visual inspection option. Building envelope tightness and insulation installation shall be considered acceptable when the items listed in Table 402.4.2, applicable to the method of construction, are field verified. Where required by the code official, an approved party independent from the installer of the insulation shall inspect the air barrier and insulation.
402.4.3 Fireplaces. New wood-burning fireplaces shall have gasketed doors and outdoor combustion air.
402.4.4 Fenestration air leakage. Windows, skylights and sliding glass doors shall have an air infiltration rate of no more than 0.3 cfm per square foot (1.5 L/s/m ) , and swinging doors no more than 0.5 cfm per square foot (2.6 L/s/m 2 ) , when tested according to NFRC 400 or AAMA/WDMAI CSA 101/1.S.2/A440 by an accredited, independent laboratory and listed and labeled by the manufacturer.
Exceptions: Site-built windows, skylights and doors.
402.4.5 Recessed lighting. Recessed luminaires installed in the building thermal envelope shall be sealed to limit air leakage between conditioned and unconditioned spaces. All recessed luminaires shall be IC-rated and labeled as meeting ASTM E 283 when tested at 1.57 psf (75 Pa) pressure differential with no more than 2.0 cfm (0.944 Lis) of air movement from the conditioned space to the ceiling cavity.
All recessed luminaires shall be sealed with a gasket or caulk between the housing and the interior wall or ceiling covering.
SECTION 403 SYSTEMS
403.2 Ducts.
403.2.1 Insulation (Prescriptive). Supply ducts in attics shall be insulated to a minimum ofR-8. All other ducts shall be insulated to a minimum of R-6.
Exception: Ducts or portions thereof located completely inside the building thermal envelope.
403.2.2 Sealing (Mandatory). All ducts, air handlers, filter boxes and building cavities used as ducts shall be sealed.
Joints and seams shall comply with Section M1601.4.1 of the International Residential Code.
Duct tightness shall be verified by either of the following:
1. Postconstruction test: Leakage to outdoors shall be less than or equal to 8 cfm (226.5 L/min) per 100 ft2
(9.29 m2) of conditioned floor area or a total leakage less than or equal to 12 cfm (12 L/min) per 100 ft 2
(9.29 m2) of conditioned floor area when tested at a pressure differential of 0.1 inches w.g. (25 Pa) across
the entire system, including the manufacturer's air handler enclosure. All register boots shall be taped or
otherwise sealed during the test.
2. Rough-in test: Total leakage shall be less than or equal to 6 cfm (169.9 L/min) per 100 ft 2 (9.29 m2) of
conditioned floor area when tested at a pressure differential of 0.1 inches w.g. (25 Pa) across the roughed
in system, including the manufacturer's air handler enclosure. All register boots shall be taped or therwise
sealed during the test. If the air handler is not installed at the time of the test, total leakage shall be less than or equal to 4 cfm (113.3 L/min) per 100 ft 2 (9.29 m 2 ) of conditioned floor area.
Exceptions: Duct tightness test is not required if the air handler and all ducts are located within conditioned
space.
It is important to you to pass the testing requirements but what if it does not?
We will conduct additional testing at no additional charge to identify the most significant air leakage locations so they can be most readily and efficiently repaired.
Infrared thermal imaging testing: provides a graphic representation of air leakage.
Smoke testing: indicates airflow patterns within the building.
Pressure pan testing: locates the air duct branch that has the most significant air leakage.
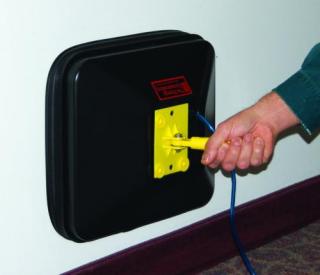
Fiber-optic inspection: reduces damage to the building in verifying leakage criteria.
Our investigative techniques get you closer to the leak source and eliminates unnecessary hunting in intrusive inspections to the building which is unnecessary and costly to mediate the air leakage.
We conduct energy efficiency evaluations in accordance with the most stringent standards: the US Army Corps of Engineers (link) requires far greater building energy efficiency requirements and we are successful in effectively identifying, documenting and recommending repairs to meet compliance standards.
Call today to discuss your energy efficiency requirements and schedule a diagnostic inspection that far exceeds a CFM leakage rate per square foot of building space.
For more information:
Phone: (615) 406-6808